[ad_1]
BMW Group has released a major announcement regarding lithium-ion batteries for its upcoming next-generation Neue Klasse electric cars, scheduled for 2025.
The German manufacturer has officially confirmed the switch from prismatic cells to cylindrical lithium-ion battery cells (as reported in May 2022), optimized for Neue Klasse architecture.
According to the company, the move to a new cell format, combined with improved chemistry and a new battery pack approach, will result in significantly better performance, lower costs and reduced environmental impact at the production plants.
The gains quoted by BMW are pretty big, including up to a 50% cost reduction on the pack level.
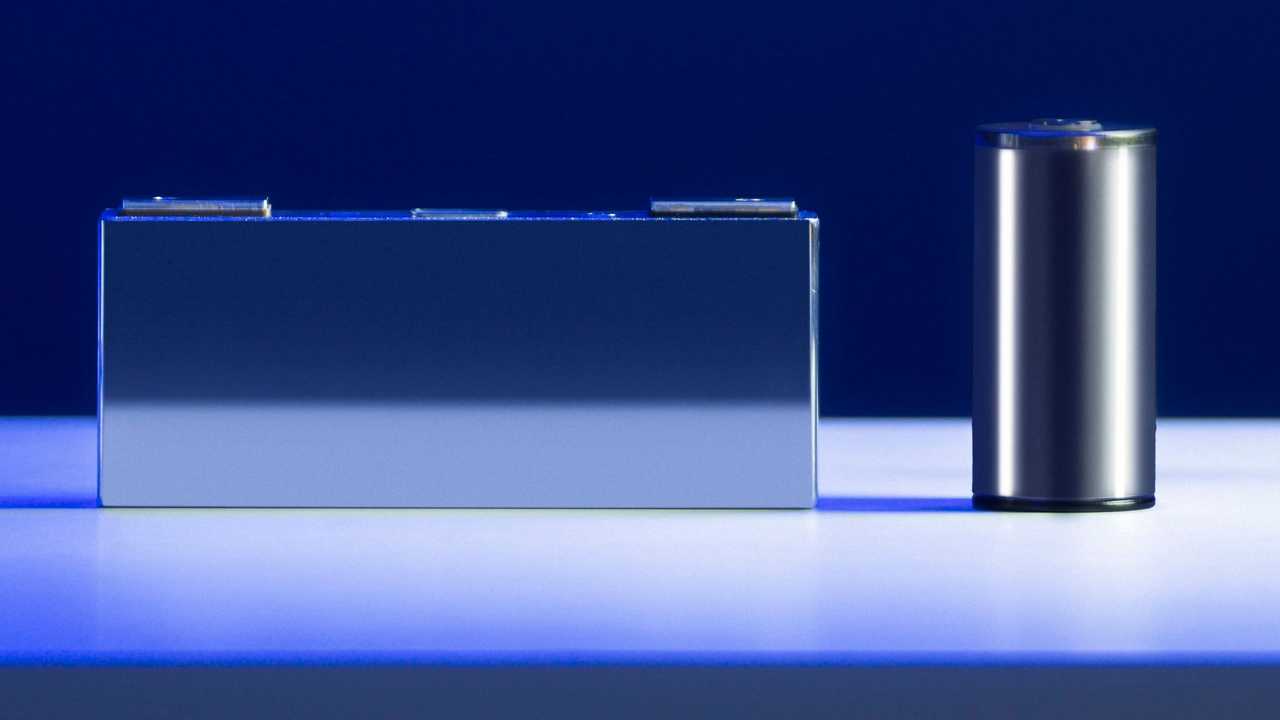
BMW round battery cell (right) side-by-side- with a prismatic battery cell (left)
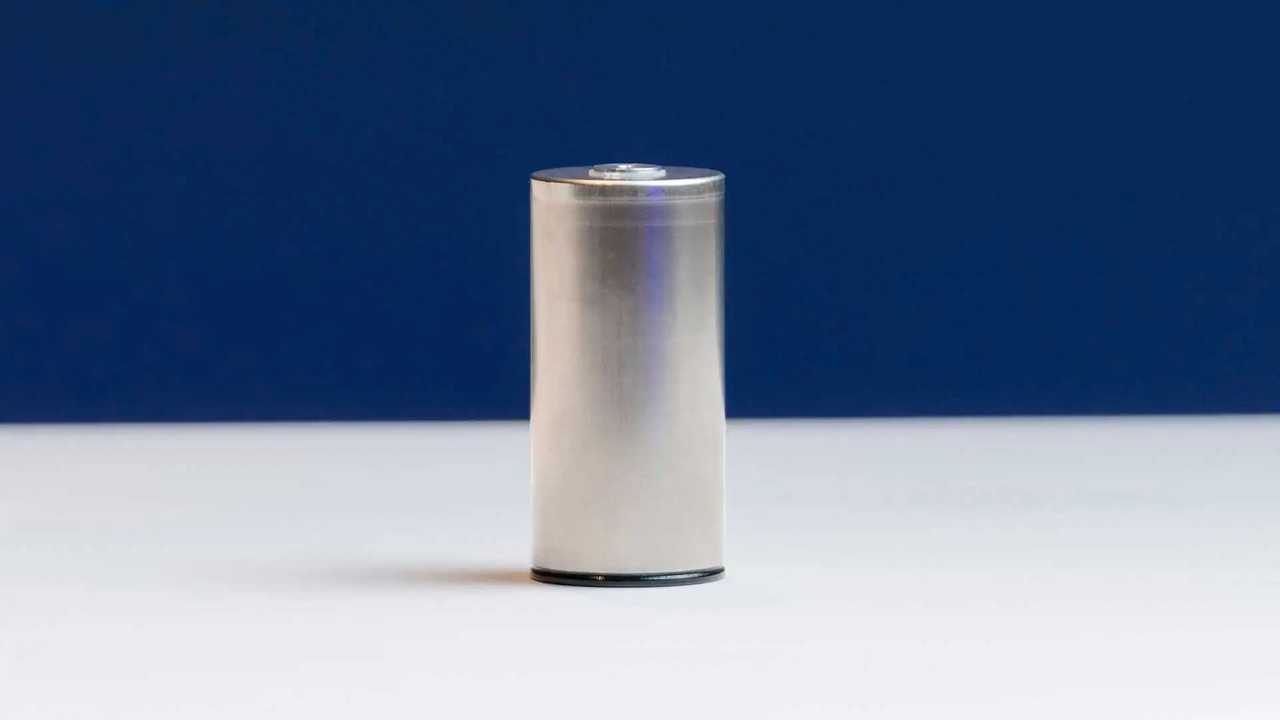
BMW round battery cell
The newly-developed “BMW round cells”, for the sixth generation of BMW eDrive technology, have a standard diameter of 46 millimeters, which is the same as in the case of Tesla’s 4680-type cylindrical battery cells (see cell analysis and pack teardown).
However, there will be two different heights, which were currently not disclosed. One of the two might be 80 mm, like in the case of Tesla cells.
According to BMW, the company has fundamentally refined the cell format, cell chemistry and pack, which compared to 5th generation prismatic batteries will result in:
- more than 20% higher volumetric energy density
(no info about gravimetric energy density) - up to 30% higher driving range (WLTP)
so potentially more than 800 km (500 miles) of range - up to 30% improved charging speed (from 10% to 80% SOC)
- up to 50% lower cost on the pack level
- up to 60% reduced CO2 emission from cell production
(through green power and secondary material)
The lithium-ion chemistry appears to still be the NCM-type, but with a higher nickel content and reduced cobalt content in the cathode. On the anode side, the silicon content will be increased.
As a side note, there will be a potential for using round LFP-cathode chemistry as well, but nothing has been confirmed yet.
“sixth-generation battery technology also offers the option of using cathodes made of lithium iron phosphate (LFP) for the first time.”
The new battery pack does not contain battery modules and might be a structural type (like in the case of Tesla’s 4680), but it would require a confirmation from BMW:
“The battery system plays a key role in the body structure of the NEUE KLASSE. Depending on the model, it can be flexibly integrated into the installation space to save space (“pack to open body”). The cell module level is thus eliminated.”
The voltage of the new battery system will be about 800 V. DC fast charging is expected to be much faster at a current of up to 500 A. It probably means that roughly 350 kW might be possible at peak.
Overall, fast charging from 10% to 80% state-of-charge (SOC) should be 30% faster than in the current, 5th battery generation.
One of the most important things is that the new battery systems (as a whole) are expected to be 50% less expensive, compared to the current fifth generation.
“By leveraging the comprehensive in-house expertise of the company’s own Battery Cell Competence Centre, the team from development, production and purchasing has been able to significantly reduce costs for the high-voltage battery, thanks to the new battery cell and new integration concept for battery technology developed by BMW.”
“Based on current market assumptions, costs can be reduced by up to 50 percent, compared to the current fifth generation. The BMW Group has set itself the goal of bringing manufacturing costs for fully-electric models down to the same level as vehicles with state-of-the-art combustion-engine technology.”
Frank Weber, member of the Board of Management of BMW AG responsible for Development said:
“The newly-developed sixth generation of our lithium-ion cells will bring a huge leap in technology that will increase energy density by more than 20 percent, improve charging speed by up to 30 percent and enhance range by up to 30 percent. We are also reducing CO2 emissions from cell production by up to 60 percent. These are big steps for sustainability and customer benefits.”
The sixth-generation BMW batteries:
- BMW round cells for Neue Klasse EVs
- lithium-ion batteries
NCM-cathode (a higher nickel content and reduced cobalt contend in the cathode, increased silicon content on the anode side)
LFP-cathode as a potential option - cylindrical cell format
a standard diameter of 46 mm
two different heights (undisclosed) - no battery cell modules
- battery pack:
potentially structural “battery system plays a key role in the body structure of the Neue Klasse”
voltage: 800 V battery system
a much higher charging capacity with a current of up to 500 A - availability from 2025
- general benefits:
more than 20% higher volumetric energy density
up to 30% higher driving range (WLTP)
up to 30% improved charging speed (from 10% to 80% SOC)
up to 50% lower cost on the pack level
up to 60% reduced CO2 emission from cell production (through green power and secondary material)
In the future, we might see also other battery chemistries used by BMW, as the company mentions all-solid-state batteries (ASSBs) coming by 2030 with a demonstrator vehicle before 2025.
“In parallel, the BMW Group is also pushing forward with development of all-solid-state batteries (ASSBs). The company aims to have high-voltage batteries of this type ready for series introduction by the end of the decade. The BMW Group will present a demonstrator vehicle with this technology on board well before 2025.”
The BMW Group intends to have a total of six cylindrical battery cell gigafactories globally, each with a total capacity of up to 20 GWh annually. That would bring us to 120 GWh total.
There will be two gigafactories in each of the three main markets: Europe, China and North American free trade zone.
- six 20 GWh battery gigafactories:
Europe: 2x 20 GWh
China: 2x 20 GWh
North American free trade zone: 2x 20 GWh - Total: 120 GWh annually
The battery plants will be built together with partners (battery manufacturers), out of which two have been already confirmed: CATL and EVE Energy. It’s not a surprise, as both companies appeared in the rumors related to cylindrical battery cells for BMW.
According to BMW, CATL and EVE Energy will build two gigafatories each, one in Europe and one in China, so already four out of six projects are set to go.
- CATL: 2 gigafactories: one in Europe, one in China
- EVE Energy: 2 gigafactories: one in Europe, one in China
- other partner/partners: 2 gigafactories in North American free trade zone
- Total: six gigafactories
The third – not yet nominated – battery partner for the cylindrical cells might be Samsung SDI, which has been BMW’s strategic battery supplier (prismatic cells) for many years and also is working on large cylindrical batteries. Not only that, Samsung SDI is working on round cells with 46 mm in diameter and two height versions (80 mm and a shorter version with a length between 40 mm to 60 mm), according to reports. That would perfectly fit into BMW’s intention of having two versions.
Anyway, the company has already awarded contracts in the two-digit billion-euro range (or USD if you wish), so the CATL and EVE Energy projects are probably underway.
“The BMW Group has already awarded contracts in the two-digit billion-euro range for production of the new BMW battery cells.
An important part of preparations to produce 46xx-type cylindrical cells will be the Cell Manufacturing Competence Centre (CMCC) in Parsdorf, near Munich in Germany. This pilot production facility will begin commissioning near-standard production of samples in late 2022.
“The pilot line at the competence centre will make it possible to analyse and fully understand the cell production process under near-standard conditions. This will help enable future suppliers produce cells to specifications and according to their own expertise – thus further optimising battery cell production with regard to quality, output and costs.”
One of the strategic goals is to reduce the CO2 emission associated with the production of batteries. The group intends to achieve a 60% reduction through the use of cobalt, lithium and nickel that include a percentage of secondary material (raw materials that are not newly mined, but already in the loop). Another thing will be electricity from renewable sources.
Joachim Post, member of the Board of Management of BMW AG responsible for Purchasing and Supplier Network said:
“To meet our long-term needs, we will be building battery cell factories with our partners, each with an annual capacity of up to 20 GWh, at six locations in key markets for us: two in China, two in Europe and two in USMCA. We have also reached agreement with our partners that they will use a percentage of secondary material for the raw materials lithium, cobalt and nickel, as well as utilising green power for production, to ensure CO2-reduced manufacturing.”
[ad_2]
Source link